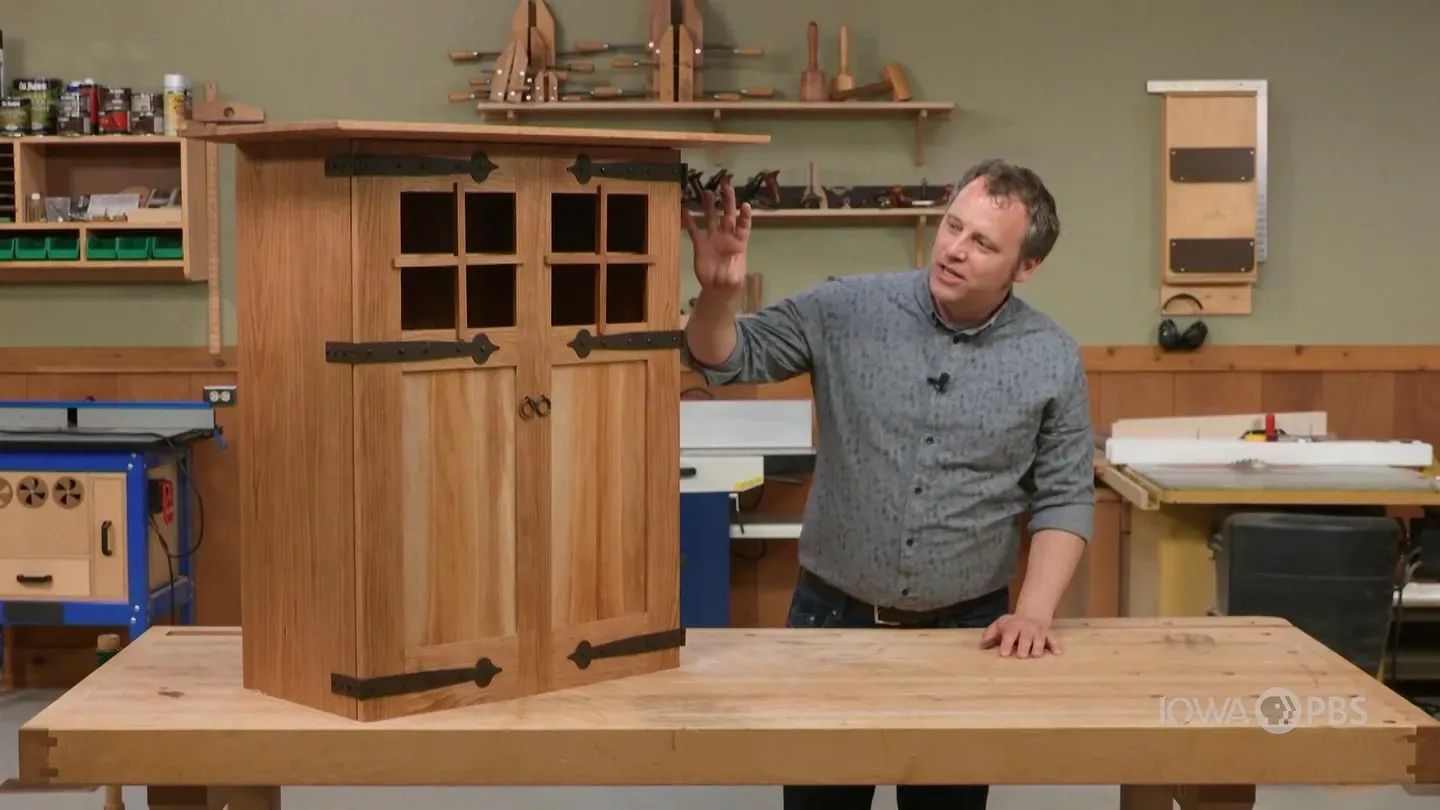
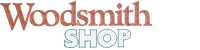
Stylish Storage Wall Cabinet
Season 16 Episode 1610 | 26m 46sVideo has Closed Captions
This project helps master essential woodworking skills you can apply to other furniture.
Originally designed as a tool cabinet, you're sure to find a home for this handsome cabinet. The project helps you master essential woodworking skills you can apply to other furniture.
Problems with Closed Captions? Closed Captioning Feedback
Problems with Closed Captions? Closed Captioning Feedback
Woodsmith Shop is a local public television program presented by Iowa PBS
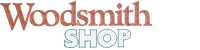
Stylish Storage Wall Cabinet
Season 16 Episode 1610 | 26m 46sVideo has Closed Captions
Originally designed as a tool cabinet, you're sure to find a home for this handsome cabinet. The project helps you master essential woodworking skills you can apply to other furniture.
Problems with Closed Captions? Closed Captioning Feedback
How to Watch Woodsmith Shop
Woodsmith Shop is available to stream on pbs.org and the free PBS App, available on iPhone, Apple TV, Android TV, Android smartphones, Amazon Fire TV, Amazon Fire Tablet, Roku, Samsung Smart TV, and Vizio.
Providing Support for PBS.org
Learn Moreabout PBS online sponsorship♪♪ Welcome again to "The Woodsmith Shop."
On today's episode, we're building this wall cabinet, and it's in the arts and crafts style but stays away from kind of your standard oak look.
We're using cherry in this version.
Now, the original wall cabinet was designed by Christopher Schwarz, an editor at Popular Woodworking.
We're adapting this design using some new techniques and some different ideas.
For example, the door panels are gonna be made from sycamore.
We're also gonna make some shop-sawn veneer for the fronts of the drawers from that same sycamore.
It adds a nice contrast and complements the look of the cherry.
There's some great ideas here for building woodworking projects, from case construction to doors and drawers.
If you want to build your own version of this wall cabinet, the plans are at our website, WoodsmithShop.com.
It's time to get things started with Chris building the case on our wall cabinet.
Announcer: Major funding for "The Woodsmith Shop" has been provided by... Old Masters -- offering wood stains and finishes for the woodworking enthusiast and professional.
And by... Kreg -- From the first cut to the final assembly, providing woodworkers with products that help to simplify woodworking challenges.
Kreg.
Additional funding provided by... Titebond Wood Glues -- the pro's advantage.
And by... ♪♪ ♪♪ ♪♪ ♪♪ Making the arts and crafts hanging tool cabinet begins by making the carcass.
Now, the carcass consists of a couple pieces -- two sides, a top, a bottom, some horizontal dividers, and finally, a shiplap back to tie it all together.
Where I'm gonna start out is with the sides, and the sides have two types of joinery, one which is going to be along the ends to bind the sides to the top and the bottom, the other for the horizontal dividers.
Now, there are a lot of different options for the joinery for the top and the bottom.
I'm gonna choose some simple router joinery because that's what we're going to be doing with all of the horizontal dividers.
The router joinery that I will be using is to create a series of four mortises in the sides for four simple tenants in the top and the bottom, and that's gonna be a straightforward, secure way to bind the sides and the top.
To do that, I'm going to be using a plunge router with a fence and a spiral up-cut bit, but before I get too carried away with joinery, let me show you about how I laid everything out.
I've got the mortises for the top and the bottom and these blind dadoes for all the horizontal dividers carefully laid out on one side, and then I've transferred them over to the other side by laying the two back to back because I don't want to create two lefts or two rights.
I want everything to be a perfect mirror image, a right and a left.
I have also done that with the ends of my parts.
So in this case, the backs are towards me, and I've transferred the lines for the mortises that I'm gonna cut from one part to the other so everything matches.
Even if I get something a little wrong, better it all be consistent throughout than inconsistent.
So let's go ahead and get the router.
I have a quarter-inch up-cut bit in it.
I have my fence set, and let's go ahead and route the mortises for the top and the bottom.
With the mortises cut in our sides, the next step is going to be to deal with the dadoes which will house the shelves in the horizontal dividers of our cabinet.
So, there's a series of these that are laid out here, and they're all half-inch wide.
Now, there is one horizontal divider which is 3/4 an inch thick, but we're gonna rabbit that to fit a half-inch dado.
That way, everything's consistent.
It'll make things a little easier for us.
One simple jig to help me route all these stop dadoes is this simple "T" square, and as you can see here, I've already started to route on either side of the "T"-square leg.
And what this does is it just shows me where the bit's going to engage our workpiece, and it makes it super easy to line my jig up with my layout lines.
So no sitting there with a ruler trying to figure out how far it is from the router bit to the edge of the router base and setting up some kind of a fence.
It's fast.
It's easy.
Works great.
The last step in prepping our side is going to be to cut a rabbit for the back.
Now, this rabbit is going to actually be an inch wide by 1/4 inch deep, and the width -- that one-inch width is to accommodate a half inch back plus a half inch for a French cleat.
And so that will allow the cabinet to sit tightly and firmly against the wall.
We won't have to worry about putting screws in through the back or anything unsightly.
French cleats are a great way to go, but it does require some space.
So I've got a tall fence set here.
I'm gonna run these vertically, and we'll go ahead and cut the rabbit now.
Cutting the joinery on the top and the bottom, forming the tenons that are going to go into these mortises, is done on the table saw with a dado blade.
The first operation that I'm going to do is to cut a rabbit on the ends of each the top and the bottom, and when I do that, I'm gonna be left with a tab.
And that tab is gonna be the thickness of the height of these mortises.
Once I have that cut, I can then come back to the table saw using a miter gauge and a tall fence, and I'll nibble away a little bit in between each of my tenons so it'll slip right into these mortises.
Well, let's take a look at the joiner that we've been working on.
First, we have the mortises in our sides, and I have taken the time to use a quarter-inch chisel and square up the ends.
Here are the tenons.
Remember, we cut a rabbit to create the thickness, and then we nibbled out in between... ...to get the spacing just so.
I'm gonna go ahead and glue up the sides, the top, and the bottom of the cabinet.
With that done, it'll be a little easier for me to go ahead and fit all the different horizontal panels that go in place, so let's start spreading a little glue.
Finishing the inside of our cabinet is pretty straightforward business.
It involves installing the horizontal dividers and a couple of vertical dividers that create the compartments for the drawers.
All of these pieces have been cut the length, so they slide in easily into the dadoes that we cut previously.
Also, you'll notice that I've notched the front corners of the dividers, and that's to give a little clearance so it will ride over the rounded end of all of our dadoes.
And that'll give it a nice, clean edge up front.
To install these, I'm gonna put just a little bit of glue in the dado and then slide my horizontal divider in.
And there we go.
So let me show you the front.
And so what we're ready for now is to put a back on our cabinet.
So I'm gonna go to the router table and prepare backing with a shiplap, and we'll get that installed.
Once that's on, we'll be ready for the top, and after that, draws and doors.
So now that Chris has the case to our cabinet done, we can go ahead and build some doors to fit.
Now, the doors, like most doors, have a couple of rails and styles.
These are gonna capture two different things.
The first is gonna be a panel on the bottom side, and in the plans, this panel is gonna be made out of spalted maple.
But here, I have kind of a different wood.
This is quarter-sawn sycamore.
It's not terribly common, but when quarter-saw, it produces this really cool kind of lacewood-looking grain.
So I think it's gonna look great on this cabinet.
Now, above that panel, there's gonna be a window.
Now, I'm gonna add some mullions into that to divide that up and really add to the Craftsman-style look.
So first thing we need to do is cut some grooves in these door parts so we can assemble this.
And the joiner here is gonna be stub tenon into grooves.
So all of our parts need a groove either on the inside edge or on these rails on both the top and the bottom edge.
So to do that...
I'm gonna go ahead and clamp the workpieces in the vise.
And now, to create the groove, I'm gonna go ahead and use my plow plane.
This plane has a fence to set the position of the cutter and has one single cutter, and you change out the cutter depending on how wide of groove you want.
Here, I want 1/4 inch.
I want the groove to be 1/4 inch deep, and I want it to be 1/4 inch from the outside edge of the workpiece.
Now it's a simple matter of setting the depth of cut to take just a small shaving, and I'm gonna start at the end of the workpiece.
I'm gonna make short strokes towards the end, working a little bit further back each time.
Once I can make full-length strokes, I'll keep making those cuts until this depth stop engages and stops my cut.
So now all the grooves are cut.
We can go and cut our tenons to fit.
To do that, I've already loaded up a dado blade here at the table saw.
Now, what I'm gonna do is use this auxiliary fence on the miter gauge to help guide the workpiece, and I'm gonna make a pass along each face.
This is gonna form the short stub tenon, and I'll do that on both ends.
And then we'll head back over to the bench and fine-tune the fit.
Okay, so now that I have all the tenons cut, I can go ahead and fine-tune the fit, because I did leave them a little thick at the table saw, and that just allows me to really hone in that fit and get a good, tight joint that will result in a good glue-up.
So to do that, I simply use a shoulder plane.
That allows me to register against the cheek and the shoulder of the tenon... and make a couple of cuts.
Then we'll test that fit.
A little snug still, so then I'll flip it over and take off a little bit of material from the other side, as well.
There we go.
That slips right in.
That's perfect.
Once we've done all that, we're pretty much ready to glue up.
The one thing I have done is I've cut these sycamore panels to size, and at the table saw, I used the dado blade to form a rabbit around the entire thing.
Now, this is gonna slip into that same groove that the tenons are gonna go in, so now it's a simple matter of gluing up the door.
♪♪ ♪♪ The plans for this arts and crafts cabinet call for installing glass on the top side of these doors.
Now, you could probably get away without installing glass, especially after you add those mullions.
It's just gonna be kind of an open-air cabinet at that point, but I am gonna go ahead and install the glass on these.
To install the glass, I'm gonna form a rabbit on the backside of the door.
I'm gonna do that here at the router table with this rabbiting bit.
Now, I've set the height so that this bearing is going to ride above the groove that's inside of the parts that are already in place, and when we cut that rabbit, it's gonna cut the rabbit all the way around the inside and leave us with rounded corners.
Once we're back at the bench, we'll just square those up with a chisel, then we're ready to install the doors to the cabinet.
So to mount the doors on our cabinet, we're using these strap hinges.
These really add to the Craftsman-style look of the piece.
So, these are just kind of laid in place... and pre-drilled, and then they're attached with these neat little pyramid screws.
So let's go ahead and install those quick.
Okay, there we go.
So now there's two final details to take care of before we hand this off to Phil.
The first is gonna be to add these mullions.
Now, these guys are simply two pieces that have been half-lapped together in the center.
Then on the inside, there are laps on the end of each piece.
This means that these will slip right into place... ...and then they can be glued in after the glass has been applied.
I think even adding a couple of dowels to the joints would make it look really nice.
Then the final thing is a pull, and to complement these big strap hinges, we have these forged ring poles.
And these are a little bit different than your standard pulls.
Instead of having a screw post, these have a large spike, and it's split.
So after you've drilled the hole, you insert this and spread out these two prongs, kind of like old paper-binding clips.
Then you can either just flatten them out so it stays in place or you can even clench these around and hammer them back on the inside of the doors.
But once those are installed, this is ready for a set of drawers.
The third part of our wall cabinet is to fill these lower compartments with drawers.
Now, I was a little inspired by Chris' work on using a router to handle all the joinery for the case.
Thought I'm gonna tackle the drawer joinery with a router, too, but here at the router table.
First things first, though, we want to size the parts for the drawers.
Now, you want to do this after the case is assembled because we want to go by what the finished dimensions are in the case.
They might vary slightly from what's in the plans.
So, for this drawer, I have the front and back here sized so that there's a small even gap across the top, and then there's just a little bit of room side to side here.
So that way, once the draw is assembled, it's gonna slide in easily.
If you try and hedge your bets here and make the drawer narrower than it should, you're more likely to have it rack than if it's closer to being a tight fit.
Now, for the joinery, I'm gonna use something called a draw joint bit, and it's kind of an odd-looking bit that works in a router table.
And what it does is create an interlocking joint that you use.
You'll route it on both the front and back, as well as the side pieces, and then once the drawer's assembled, the pieces kind of self-register with each other, creating a square assembly and one that's gonna stand up to a lot of use.
So, for this one, I've set the bit.
They all kind of have a magic height setting at about 3/8 of an inch, but it's still a good idea to use some test pieces.
And then for the bit projection from the fence, I used one of my offcuts, and the bit needs to project from the fence to match the thickness of the sides.
It's pretty easy to do.
Now, what I'm gonna do is make a pass across both ends of the drawer fronts and backs.
Now, I don't want these pieces to wobble in the middle of the cut, so I'm gonna use one of my scrap pieces here as a backer board.
And then that's also gonna prevent tear out as the bit exits the cut.
Things are a little different for routing the joint on the drawer sides.
Now, the bit height stays the same.
What we need to do is adjust the fence, bringing it forward a little bit so that the bit creates a small groove on the inside faces of the sides.
In order to do that, we're gonna change the orientation of the sides, too.
I'm gonna run it vertically against the fence as I go along.
The key thing here is keeping it snugly against the fence for a consistent depth of cut.
After completing work at the router table, I headed over to the table saw, set up a dado blade, and cut the groove that's gonna hold the drawer bottom.
And you could do a dry assembly and cut the plywood drawer bottoms to size, which brings us to this point, assembling the drawers.
♪♪ ♪♪ ♪♪ The poplar we used to make the drawer boxes works really well.
It cuts easily.
It's got a really smooth consistency.
It's not that attractive, so to dress things up, we're gonna apply a thin piece of sycamore veneer to the drawer fronts.
And that's gonna match the panels in the doors.
Doing this is pretty simple.
It's just a matter of cutting those to their rough size and then gluing them in place.
But there's something else we want to consider, and that's the drawers are arrayed in sequence across.
So what I'd like to have is the grain from the veneers to run across the two drawers in each pair.
This is gonna help the inside of the cabinet look its best.
After getting the veneer glued on to the front of the drawers and letting it dry, we're ready to trim it flush.
Now, my favorite tool for the job here is to just use a regular block plane.
I have a little one here, and there's a specific order you want to do in order to get the best results.
I start with trimming the end grain on the edges of the drawer, but what you want to do first is kind of knock off, dock these corners a little bit... with the block plane.
And that's the stroke that I want to use where I'm going both down along the veneer and into the body of the drawer.
That's gonna help prevent any chipping on the front edge of the veneer.
Once you have the ends flush, then I can rotate the drawer, and I'm just bumping it up against a couple of bench dogs here.
And then I can take long... ...long strokes along the top and bottom of the drawer.
And I can flip it around as I need to to go with the direction of the grain and again, avoid tearing on this edge.
The last thing that I want to do while I have the block plane out and now that the veneer is all flushed up is I want to just soften the edges around the veneer with a very light couple of passes.
There.
Now the drawer slide into place.
The edges are kind of friendlier to the touch, and they still have that little bit of a chamfer on there that's gonna catch the light.
Now that the draws are wrapped up, it's time to talk about finishing our wall cabinet.
It's your last opportunity to go over the project with a fine-tooth comb, and the usual litany of precautions apply here on sanding.
You want to make sure you get rid of any glue squeeze-out and any scratches that you don't want showing up in the final project.
So, the finish that I'm using is a tung-oil varnish, and what I like about it is that it's like a thinned varnish.
So it builds up to a nice finish, and it offers some really good color to the materials.
And you'll see that as soon as I apply it here.
I'm just using a foam brush, applying a good amount to... the surface here...on the front, and then I want to be really careful on the edges... ...basically just to get the veneer.
After applying the finish, you want to wipe down the excess... ...so that when it dries, it's gonna be a smooth, durable film.
If you don't, it can be a little bit gummy and tacky on there.
So now we can set this aside and begin work on the doors.
Now, I usually follow the same order that you would on a door as you would when you're painting, and I'll start with the rabbited frame here.
Next, I'll move on to the sycamore panel on the bottom part of the door.
Then we'll do the rails... ...and finish up with long strokes flooding the styles.
Now, when it comes to the case, the same kind of application principle applies.
I'm gonna brush on a liberal coat all along the sides and the top of the case.
On the inside, you can be a little bit more... discreet on how you do it because I don't need to have finish all the way inside the drawer pockets, so I'll just apply finish on the faces of the dividers and shelves that Chris installed.
Up top, where the two open shelves are, that's where I'm gonna apply finish all the way to the back.
There's nothing quite like the feeling of seeing a project once it all comes together, especially something like this wall cabinet, where we have the doors, drawers, and the hardware that all need to come together at the very end, and you can see it turned out to be a great-looking project.
We have a nice use of materials between the cherry case parts, the sycamore door panels and drawer fronts, and how they all work together with the cool hardware that we selected.
Now, what I like about wall cabinets is that they offer a lot of woodworking lessons in a relatively compact package.
We have some casework in making the case itself, building doors and drawers, all mini projects in their own.
If you want to make a wall cabinet like this, the plans are at our website, WoodsmithShop.com.
You'll also find a variety of other plans, project ideas, and videos to help you become a better woodworker in your own shop, and then we'll meet right back here in the Woodsmith Shop.
♪♪ ♪♪ ♪♪ If you'd like to get more video tips and techniques, sign up for the free weekly Woodsmith eTip.
Every week, you'll receive an e-mail with a video tip to get more out of your table saw, router table, and more.
Sign up at WoodsmithShop.com.
Everything in today's show comes from the newly expanded Woodsmith Guild Edition, with shop projects, plans, tips, and techniques.
To get a free preview issue of the Woodsmith Guild Edition and a free Woodsmith book, go to WoodsmithShop.com.
In addition, past seasons of "The Woodsmith Shop" are available on DVD, or you can watch them online from your computer, tablet, or mobile device.
For more information, go to WoodsmithShop.com.
Announcer: Major funding for "The Woodsmith Shop" has been provided by... Old Masters -- offering wood stains and finishes for the woodworking enthusiast and professional.
And by... Kreg -- From the first cut to the final assembly, providing woodworkers with products that help to simplify woodworking challenges.
Kreg.
Additional funding provided by... Titebond Wood Glues -- the pro's advantage.
And by... ♪♪ ♪♪
Support for PBS provided by:
Woodsmith Shop is a local public television program presented by Iowa PBS